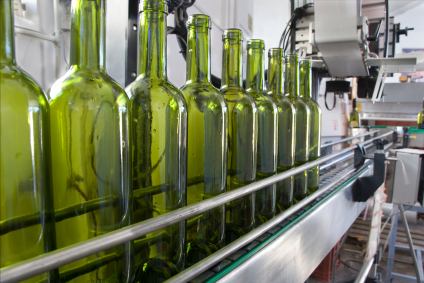
One of the most overlooked areas of any pneumatic filling machine is the solenoids. These devices directly operate the filling head to start and stop the flow of a medium. They operate with pneumatic pressure which is controlled through an electrical signal, sent from the control panel or PLC.
Once a flow sensor or other sensor reads that the bottle is full, a signal is sent to the solenoid and air is either supplied or removed from the fill head to stop the flow. Because of the inherent dynamics of solenoids, there will always be a delay, or response time, between the signal and the flow of air changing states on the fill head.
Most machines can be calibrated to compensate for this delay. Let’s assume that your target fill volume for a 500 ml bottle is 505 ml, taking into account evaporation on the store shelf, and you know that a signal sent when the bottle is at 499 ml will actually fill till 505 ml because of the response time of the solenoid. This situation will be acceptable for the entire machine if all of the solenoids have the exact same response time but most solenoid manufacturers are either unable or unwilling to calibrate each solenoid to provide the same response time.
MAC Valves, however, has developed a process that during manufacturing each solenoid used for a filling application can be calibrated to have a response time with a variation of only ±0.2 ms between valves. What this means is that while a standard machine running non-MAC Valve solenoids will have on average 10 ml of additional overfill per bottle, when the same machine is converted to MAC Valve solenoids there is only a 2 ml variation across the entire machine. This will directly translate into thousands of dollars a year of savings depending on the cost of medium and the quantity of bottles filled.
For more information about Filling, please contact your local MDN distributor